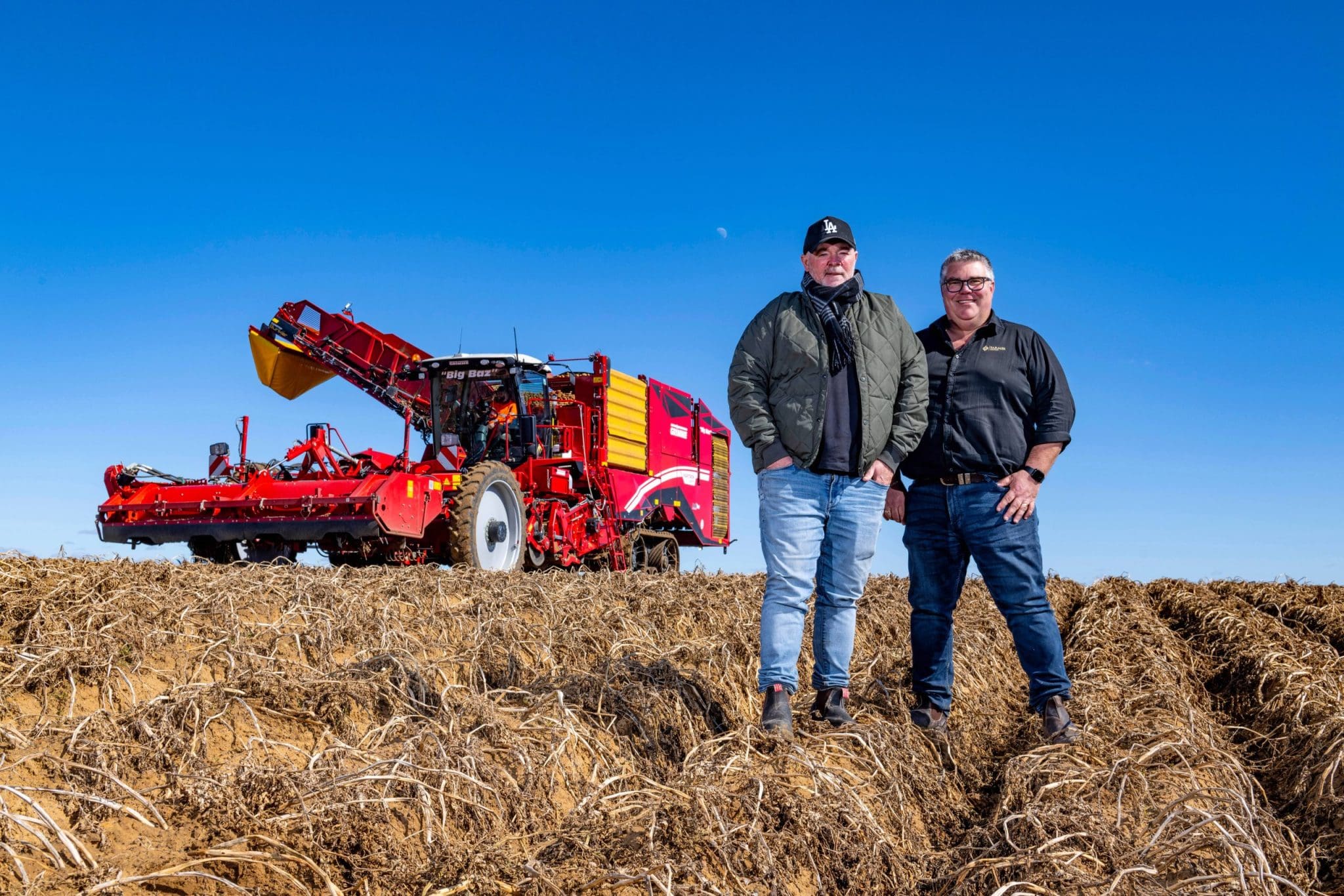
THE vision of innovative South Australian washed potato grower, the late Barry Farmer, has been fulfilled with the delivery of a state-of-the-art GRIMME VARITRON 470 self-propelled four-row harvester to the Farmer Group’s Kangaringa Station.
The harvester – affectionately dubbed ‘Big Baz’ – is capable of gently lifting, cleaning and loading up to 45 tonnes of potatoes per hour, perfectly complementing the capacity of the company’s state-of-the-art robotic washing plant at Virginia. The Farmer Group grows about 65,000 tonnes of washed potatoes, 20,000 tonnes of onions and 400 tonnes of almonds, in addition to its extensive beef and wool growing enterprises across 32,000 ha of holdings.
Farmer Group General Manager, Jason Kirk, says the harvester ‘ticks all the boxes’ for performance, efficiency and quality. “Technology is important to us and we think GRIMME is the best technology available for growing potatoes and onions,” he says. “The Farmer family has been using GRIMME planting and harvesting equipment for 35 years. If we can do something more efficiently or with less staff, then that’s something we’re interested in. This machine can comfortably dig between 250 and 300 tonnes of potatoes every day, five days a week, which is more than enough capacity for big order days at the wash plant.”
The harvester has significantly reduced labour requirements. “This machine has replaced two trailing harvesters that require two tractor drivers, up to eight graders on the back and another in a tractor with a slasher,” Jason says. “With the VARITRON, we’re doing the same job, faster and better, with just one person. We have already clocked up more than 2000 operating hours on the new harvester, so that’s a huge saving. There’s also another important benefit in OH&S, particularly if you have staff who may not speak English as their first language.”
Kangaringa Station Operations Manager, Simon Samon, who has nearly 40 years’ experience growing potatoes, is rapt with the new harvester. “It’s absolutely fantastic – it’s so smooth and efficient,” he says. “Yesterday, a crew of three harvested 144 tonnes in five hours without raising a sweat. I didn’t think we could get this sort of efficiency whilst maintaining quality but it’s extremely gentle on the spuds.”

The harvester features an all-German drive train, with a 460 horsepower Mercedes-Benz OM 470LA engine powering two CLAAS TERRA TRAC tracked assemblies. With a contact area of 1.6 square metres, the 800 mm rubber tracks ensure a smooth, fast and safe harvest in all conditions. “The tracks are way more comfortable than tyres but the big thing is flotation,” Simon says. “We irrigate every day and this is a great place for harvesters, tractors and trailers to get bogged. “The hydro-pneumatic suspension and automatic levelling is also pretty handy if you’re on a slope or going up or downhill. Another bonus is that the tracks provide a consolidated path for the following tractor and trailer.”
The hydraulically-driven intake web, first main web and second main web have enormous sieve areas, adjustable pitch angles and independent speed adjustment. “When you’re harvesting potatoes, dirt is your friend,” Simon says. “The VARITRON 470 carries a mountain of dirt up the web with the potatoes before the twin separation trays do their job. They also remove any organic waste picked up with the spuds, so that’s less transport costs.”
Set on a 75 cm row width, the intake web has a width of 2.97 m and a sieve area of 4.1 square metres. This is complemented by a further 12.8 square metres across the first and second webs. Set on a 90 cm row width, the width of the intake web increases to 3.6 m and the total sieve area to 18.1 square metres. All three webs, along with the fine haulm elevator and ring elevator, are reversible. Likewise, the speed of the 1200 mm wide ring elevator is automatically adjusted according to load.
The VARITRON 470 also features a seven-tonne, ‘non-stop’ bunker that allows continuous unloading. The auto-reversing bunker automatically discharges potatoes back into the bunker once the elevator is deactivated. Despite its 15 metres length, the VARITRON 470 is remarkably nimble at the headlands. Fitted with 270/95 R54 tyres, the front wheels have a 63-degree steering angle while the rear tracks have a 15 degree steering angle. The front wheel span can be adjusted from 3.49 to 3.85 m to suit a row spacing of 75 to 90 cm.
The high visibility, spacious cab is equipped with automatic climate control, suspended leather seat, electrically-adjustable folding mirrors, audio system with Bluetooth connectivity, wipers on all windows and a sun visor. Key functions are controlled using a multi-functional customisable joystick and a 30 cm touchscreen display. “It’s just so easy to operate,” Simon says. “Yes, it’s got automatic speed adjustment but we prefer to manually adjust the speed of the webs, separator trays and elevator speed so that we have total control. Between the windows and the cameras, the operator can see everything. It is incredibly quiet, both inside and out. The hydraulics make more noise than the engine. The loudest thing on this machine is the beeper when it reverses.”