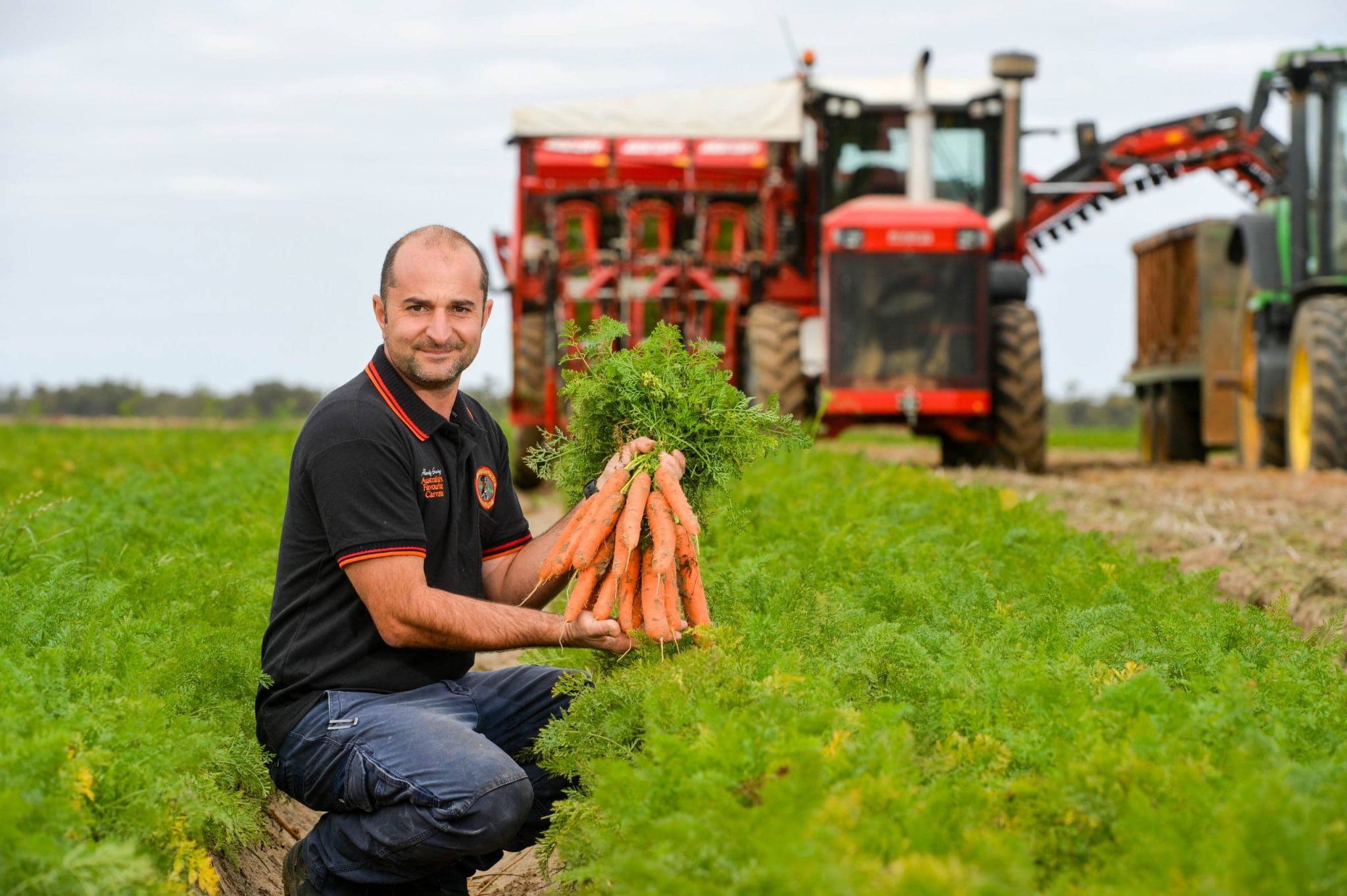
A SELF-propelled three-row harvester is driving harvesting efficiency to new levels for one of Australia’s largest carrot growers, Lamattina & Sons. Harvesting five days a week, 52 weeks a year, this family-owned and operated business processes more than 1000 tonnes of carrots every week for delivery to a range of retail, wholesale, processing and export markets. Powering this productivity is an ASA-LIFT SP-305-SFH self-propelled three-row harvester purchased last August. Trundling along at 3.5 km/h, the machine is capable of gently lifting, cleaning and loading more than 45 tonnes of carrots an hour.
Lamattina & Sons, which was recently named AUSVEG Victoria’s Vegetable Farm of the Year, has a long and close relationship with ASA-LIFT, which is recognised as a global leader in vegetable harvesting technology. “Dad purchased his first linkage-mounted, single-row harvester in the 1970s and then a self-propelled double-row harvester in 1986,” John Lamattina says. “This is our eighth ASA-LIFT harvester and there’s another coming at the end of the year. For a long time, ASA-LIFT didn’t have an Australian distributor, so we dealt directly with the company’s owner, Peter Søerensen, and then his son, Laust. They’ve visited our farms with their team many times over the years and we have always made it a point to visit the ASA-LIFT factory to inspect our new harvester before it’s shipped.”
In 2020, the Danish company was acquired by German manufacturer, GRIMME, itself recognised as a global leader in potato and beet planting, harvesting and handling equipment. Both brands are represented in Australia and New Zealand by Landpower Vegetable Centre. The Lamattinas’ new harvester has been highly ‘specced’ with optional hydraulic dirt ‘knockers’, twin bearings on the back knives, protective shields on the auto-greaser system and a customised ‘hedgehog’ belt. “All of these little ideas seem insignificant but they are based on decades of experience,” John says. “We’re a long way from Landpower in Melbourne and even further from the factory in Denmark, so we’re big on reliability and longevity. We expect to get 5000 hours out of the elevator belt and 1500 hours out of the knives, which is probably two or three times the norm.”
The Lamattinas also customised the conveying system. “We opted for a lot of electronics, such as sensors on every belt,” John says. “This means we can run each belt at exactly the right speed to protect crop quality and maximise belt life. If the belt speed is going 20% too fast, you’re going to damage the carrots and wear out a $30,000 belt 20% sooner. We had some of the belts reconfigured to a bigger size to cope with the higher capacity. We also asked for some of the belts to be left at the same size as our existing harvesters so we could utilise our spare parts inventory.”
Carrots are loaded directly into trailing bins. “We didn’t want a bunker because it’s another step that can damage the crop,” John says. “If necessary, we would rather stop the harvester and wait for the next trailer to arrive.”

The unloading elevator, which is remotely-controlled by the tractor driver, can be adjusted laterally by up to 30 cm to ensure each bin is evenly filled. Bin weight is monitored using load cells in the trailer. The delivery of a second SP-305-SFH later this year will signal the retirement of the Lamattinas’ two existing harvesters, which have clocked up an impressive 22,000 working hours between them. “Our philosophy has always been to buy the best, utilise it to its full capacity, maintain it properly and then replace it when it’s done,” John says. “People gasp when I tell them this machine cost us about $1.2 million – but it paid for itself in six months compared to hand picking. Before he got his first harvester, Dad used to pick five bins a day. Now we’re doing that in less than a minute.”
Over the past 30 years, Rocky and Kathy Lamattina, together with their three sons, Angelo, Phil and John, have built a world-class operation employing more than 120 staff and contractors. The next generation will soon join them. “Dad started off growing broccoli, potatoes and carrots,” John says. “One day he said that we were going to focus on just one crop and become very good at it. That crop was carrots and we wanted to grow them 12 months of the year – and that meant diversifying geographically.”

The business now operates three properties at Wemen and Kaniva in northern Victoria and St George in southern Queensland. More than 2400 ha has been developed to irrigation, allowing about 600 ha of carrots to be planted each year. The harvesting season runs from February to July at Kaniva; August to October at St George; and then from August to January at Wemen.
Harvested carrots are transported back to Wemen, where they are washed, graded, packed and dispatched. A strict crop rotation program and the use of compost to boost soil organic matter levels have helped to push average yields to about 85 t/ha, well above the industry norm of 50–60 t/ha. “Carrots are the cheapest vegetable on the shelves and that hasn’t changed in 30 years,” John says. “Our only option has been to become more efficient. We’re producing the same amount of carrots as we did 10 years ago but planting about 120 ha less. In turn, that’s 360 ha less cereals, mustard and sorghum crops that we have to grow, not to mention all the crop inputs, water and diesel. Consumers talk about sustainability – well, this is what it looks like at the coal face. Plus we’ve worked hard on quality. We put in optical graders five years ago so we can deliver exactly what the customer wants in terms of size, weight, colour and grade, which has significantly reduced our waste.”
Each carrot crop is followed by barley or wheat, mustard and then either field peas or sorghum. “The break crops help to keep the soil cover together, plus it allows us to break weed and disease cycles,” John says. “The cereal and sorghum add organic matter, brassica is a natural fumigant against nematodes and the field peas add nitrogen to the soil. We treat the cover crops like we treat the carrots. We fertilise, spray and irrigate them just like a normal crop – but then we mulch them straight back into the ground! Most farmers can’t get their head around a green manure crop but you can’t put a price on its value. The sorghum alone is adding more than 20 t/ha of dry matter to the soil.”